MakeRight
Removing the Barriers of 3D Printing
for Everyday Consumers
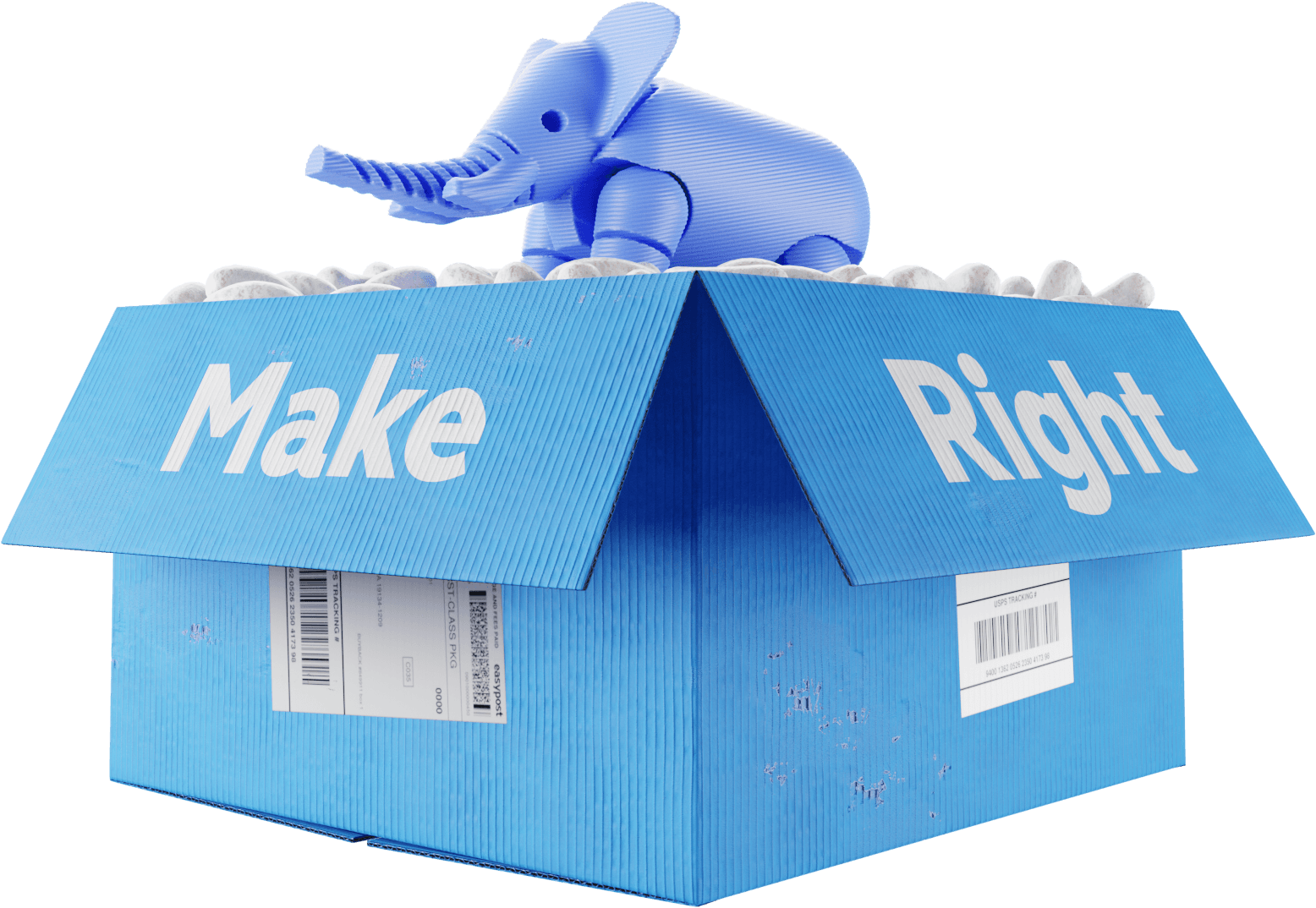
DESCRIPTION
For my undergraduate capstone, I created a service that directly connects owners of 3D printers to customers in need. Based on a gig economy model, this service enables access to 3D printing without the barriers of cost, and know-how.
DELIVERABLES
- Hi-fidelity prototypes,
of 2 user flows - 30+ Unique screens
ROLES
- UX/UI Designer
- UX Researcher
- Frontend Dev
- Graphic Design
TIMELINE
6 Months
TOOLS
BACKGROUND
3D printing is yet to reach
its full potential
Offering endless customization, cheap manufacturing, and fast production speeds.
3D printing has a vast potential to benefit everyday consumers.
In the early 2010s, we were told they would be found in every home; giving consumers the power to create anything. But, its barriers were too great to reach these expectations, and this reality fell flat. Now, 3D printing hardly has any impact on the average consumer’s life.
CHALLENGE
Cost, and technical knowledge prevent mass adoption
Owning a 3D printer is a steep upfront investment, and learning to use it is a massive time-sink. Even then, users without 3D modelling experience will still be restricted to premade objects.
OPPORTUNITY
How might we remove these barriers, and translate the benefits of 3D printing to the average consumer?
SOLUTION
Connect consumers with owners of 3D printers
for stress-free, low-cost production
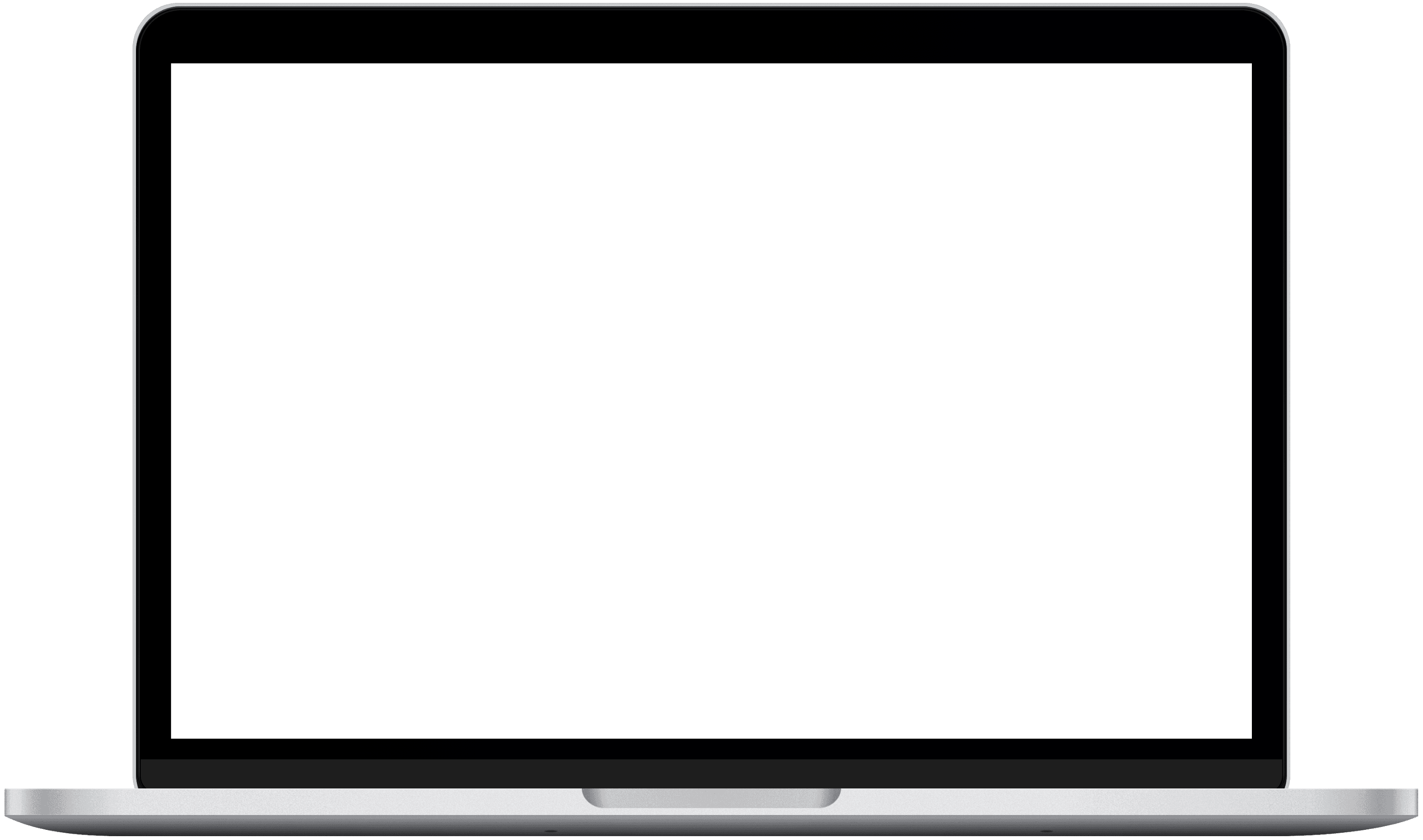
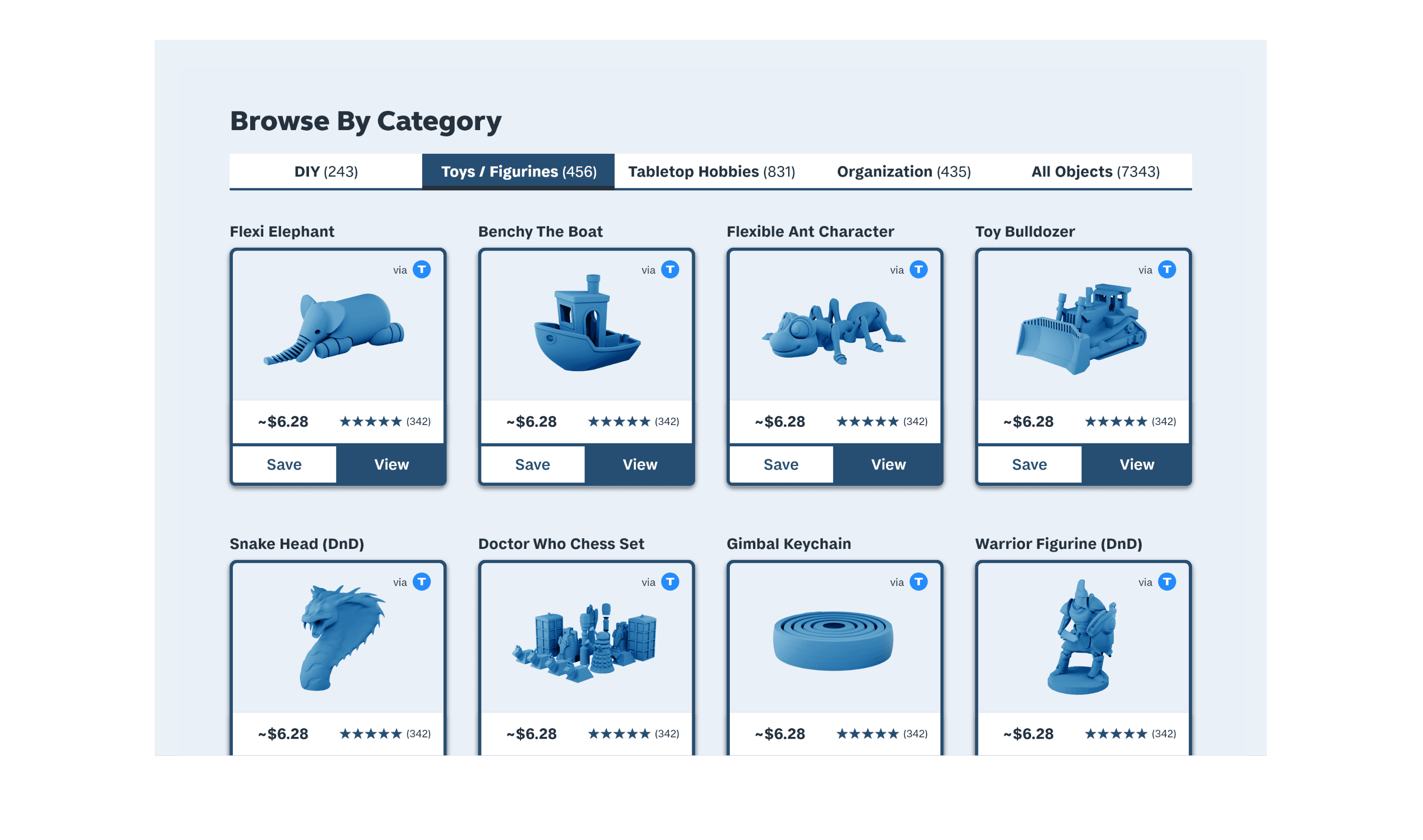
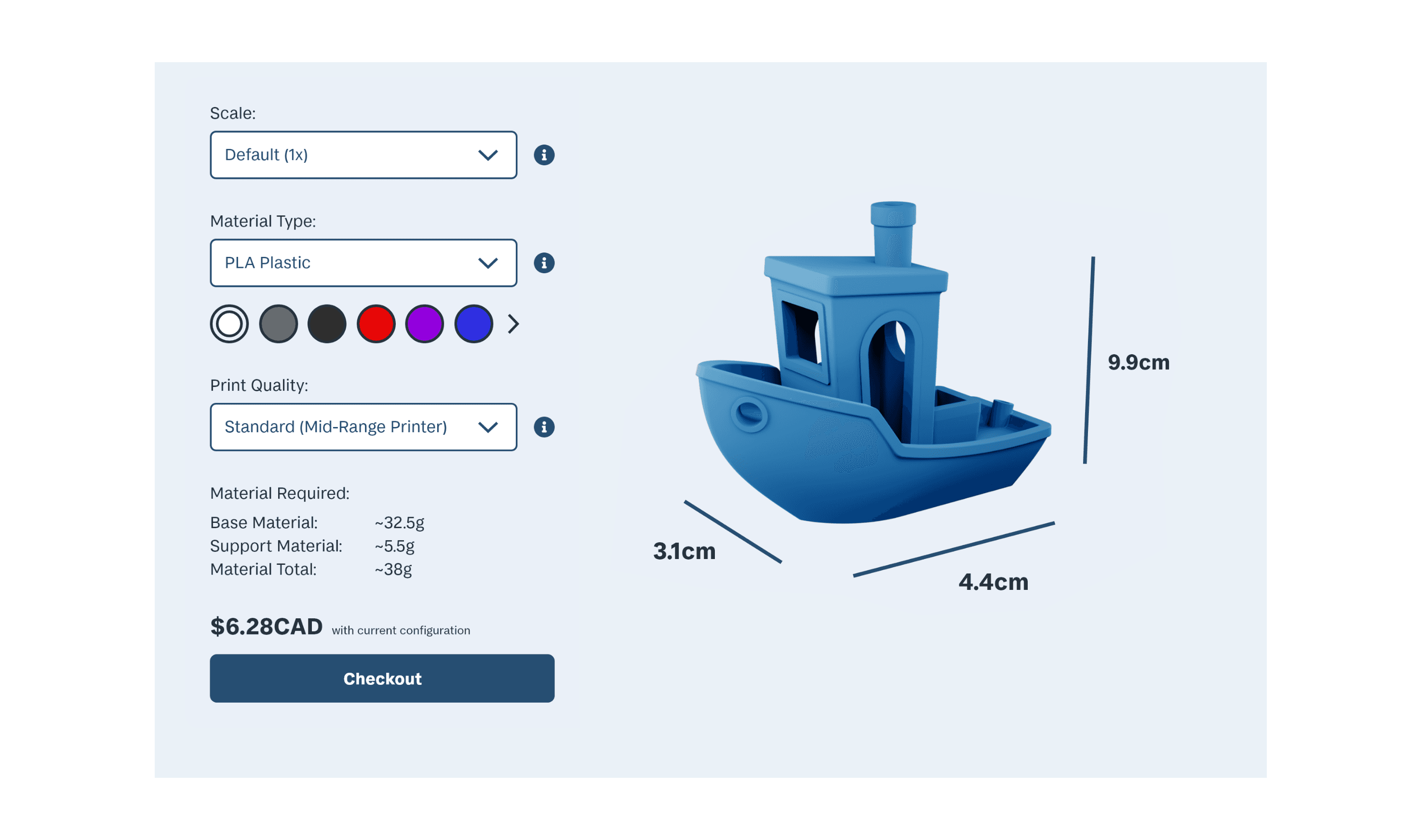
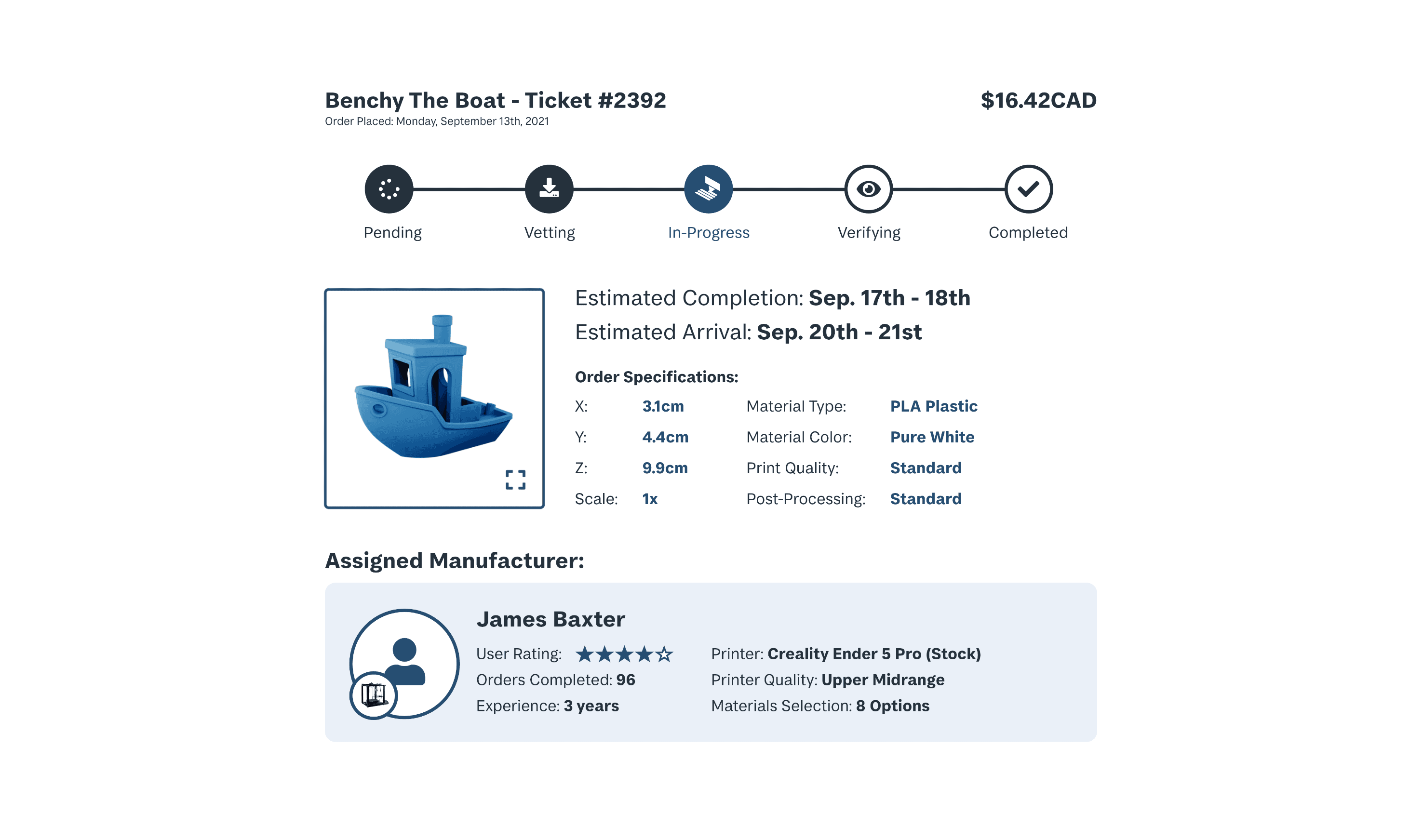
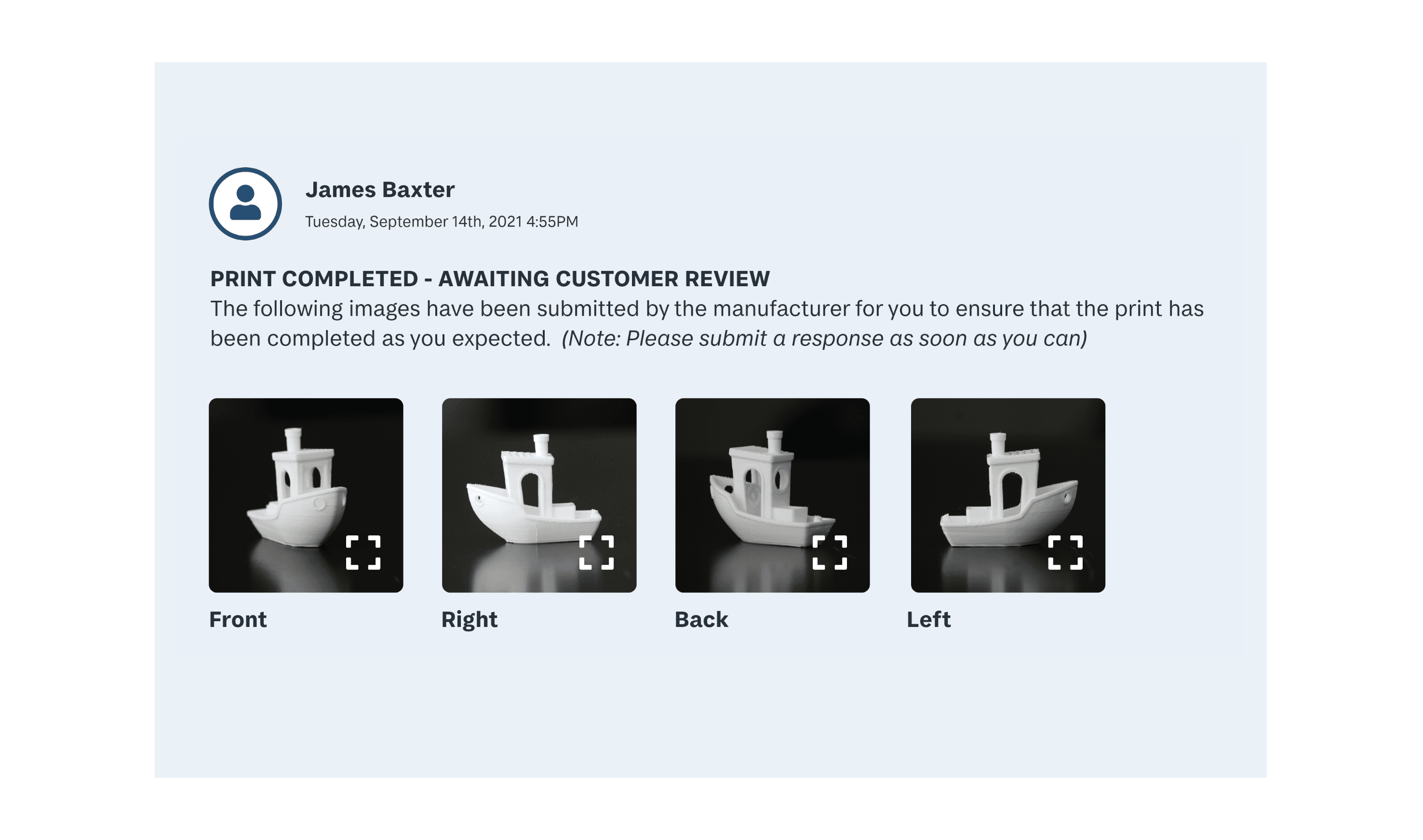
Choose
from a storefront of sourced 3D models, or upload your own
Choose
from a storefront of sourced 3D models, or upload your own
Tweak
and personalize
to suit your needs
Tweak
and personalize
to suit your needs
Order
your print, automatically
assigning it to one of our
verified makers
Order
your print, automatically
assigning it to one of our
verified makers
Receive
the purchased item right at your front door
Receive
the purchased item right at your front door
Slashing the overhead of competitors
Competing services ruin the low-cost benefits of 3D printing by charging steep overhead fees. This results from countless technicians and machines operating under one roof.
MakeRight undercuts this overhead by connecting customers directly to makers. Clients are only charged for the work of one technician, running their own equipment.
Operating much like an ‘Uber’
for 3D prints from local makers
Customers gain access to 3D printing’s low-cost, customizable production, without owning or operating the technology. In parallel, hobbyist makers now have an accessible platform to profit off their equipment and skills.
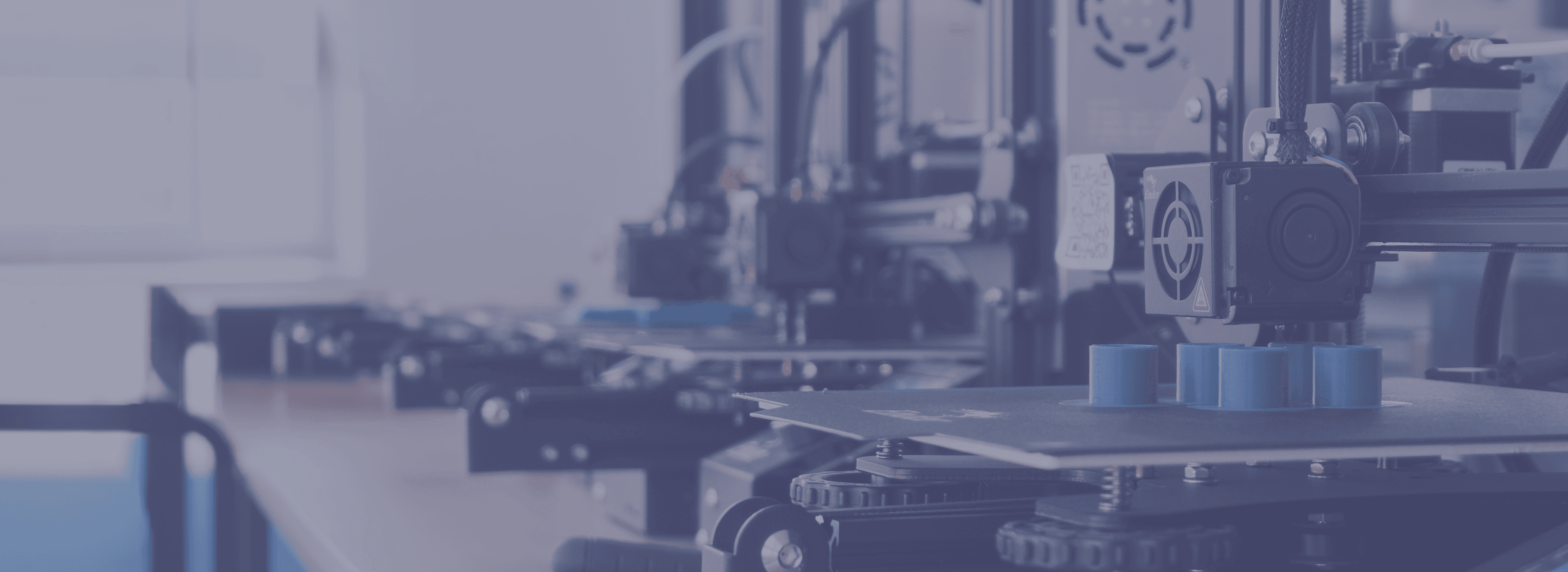
Building MakeRight
PROJECT PLAN
Project phases and timeline
APPROACH
Finding a focus within the field of 3D printing
Secondary research
for high-level context of the 3D printing world
Interviews & surveys
to understand users’ experiences at a lower level
SECONDARY RESEARCH
Cost and knowledge gaps prevent widespread use,
while hobbyist printers sit idle
What factors limit the adoption of 3D printing?
Hobbyists often surpass
these barriers out of passion
Only to have their printer sit idle most of the time
PRIMARY RESEARCH
Interviews with 4 makers, and 6 laypersons
corroborated these statistics
Non-printer owners have interest in the tech, and barriers
to accessing it
Despite identifying benefits of using 3D printing, these architecture students avoided it due to intimidation.
Even though, through their school, they had open access to printers.
“...In architecture, some calculations are easier when
you have a real model vs. digital...” - Layperson #6
“But I never use [3D printing] because I don’t know
how to work the machines.”
- Layperson #4
While many owners of 3D printers have idle machines, and free time
Owners’ usage depended partially on free time, but mostly on current needs and projects.
Meaning there was frequent overlap between their idle printer, and free time, due to a lack of printable ideas.
“How often do you use your printer?” - Me
“Not enough” - Owners #1-4, unanimously
‘AHA’ MOMENT
Idle printers,
potential for wider use
Primary and secondary research had converged on these 2 key takeaways. I knew my solution would be found at their intersection.
- The machines of skilled printer owners are largely idle
- Laypersons feel barred from 3D printing, despite having
several ideas and uses for the tech
METHODOLOGY
Moving from problem to solution
Brainstorming
to generate a wide number of potential solutions
Refine ideas
to fully explore promising concepts
Focus group
to gauge reception and feedback from users
REFINE IDEAS
I expanded on this chosen idea by considering:
Goals
How This Might Be Addressed
Concerns
Focus group testing on the newly refined concept
allowed me to gauge reception, and gather feedback
FOCUS GROUP TESTING
Discovering a promising enthusiasm, and some important concerns
I gathered 6 laypersons, and 4 printer owners, and asked each group questions surrounding my proposed service.
At the end of the test, I revealed the concept. I then asked more specific questions, collected feedback, and supported their discussion with prompts and clarification.
Reception was quite positive among both groups:
Laypersons commented ideas for what they would print, while makers showed excitement towards profiting off their equipment.
“I think a business like this could totally work... ...I think there’s a lot of people with printers and free time that would hop on an opportunity like this.” - Maker #2
“I would definitely use that service. Not having to set up and use a printer myself? I would print so much stuff!”- Layperson #4
With important concerns being raised, as well:
Distribution of responsibilities
Draw a line separating the responsibilities of makers, and customers.
“It’s a question of distributing responsibility. There’s 2 types of problems: maker problems, and customer problems.” - Layperson #3
Ensure a viable work experience for makers
Appropriate deadlines for printers, with some kind of flexibility.
“There’s a lot of little steps and things that go into making the print that can take time.”- Maker #3
3D modelling adds too much complication
Model creation and design is a whole service in itself; including it in the service would drastically affect scope.
“I can’t model things for people, so I’m not very interested in that side of the service.”- Maker #3
With a foundation of research, and validation from testers, it was time to begin prototyping
METHODOLOGY
Prototype scope covered the core journey of makers
and customers
The two journeys included all the main touch-points from sign-up to order fulfillment. This development goal would allow me to establish the foundation and core interactions of the service.
METHODOLOGY
The workload was divided
across 4 project phases
I broke development into 4 phases of 4-6 weeks.
Each containing its own cycles of development, testing, and iteration.
Phase 1:
Maker Journey, Low-Fi
Phase 2:
Customer Journey, Low-Fi
Phase 3:
Maker Journey, High-Fi
Phase 4:
Customer Journey, High-Fi
PROJECT ITERATIONS
Progression & refinement
Customer Journey - Item Listing (Low-Fi)
Phase 1
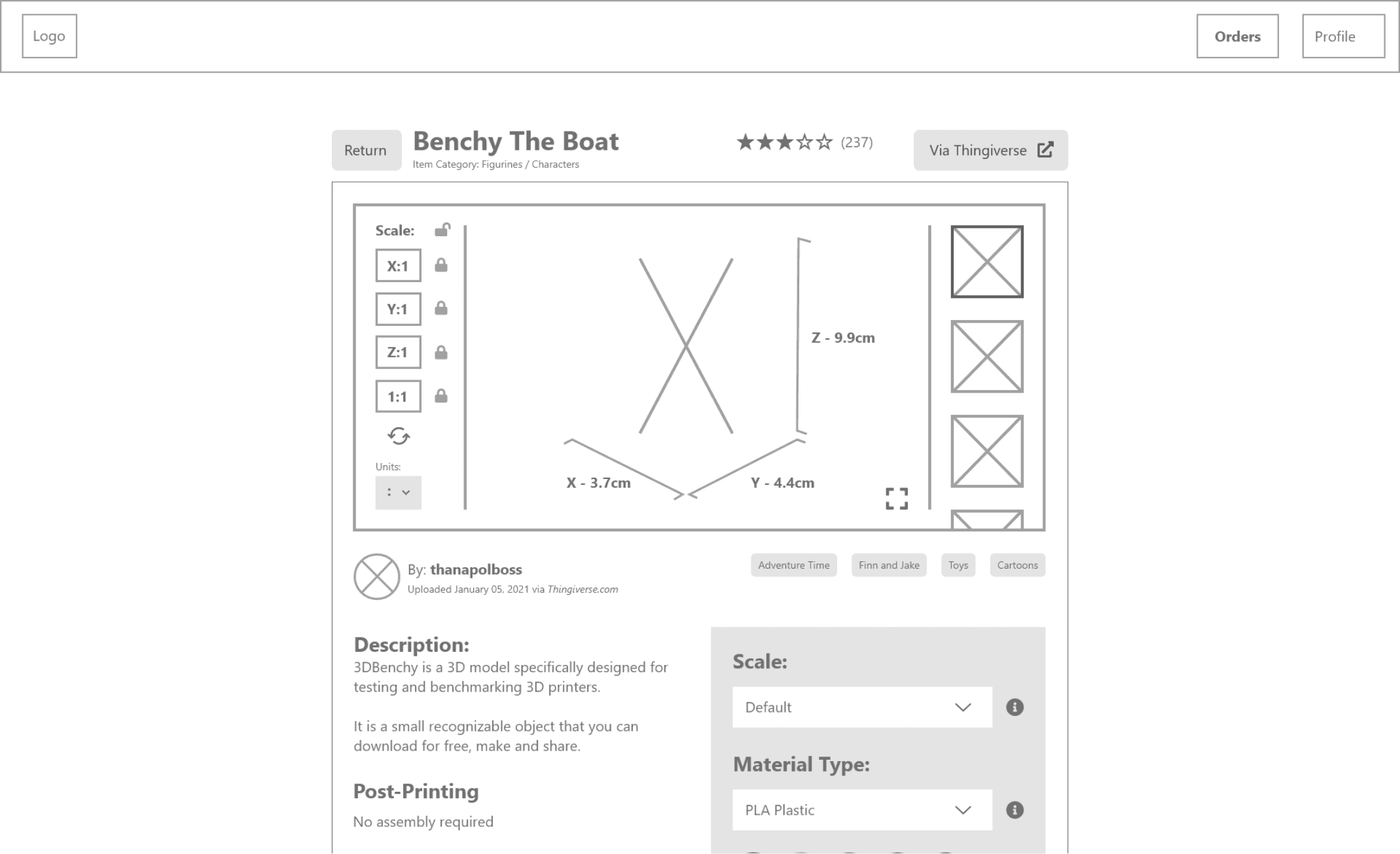
Customer Journey - Item Listing (High-Fi)
Phase 2
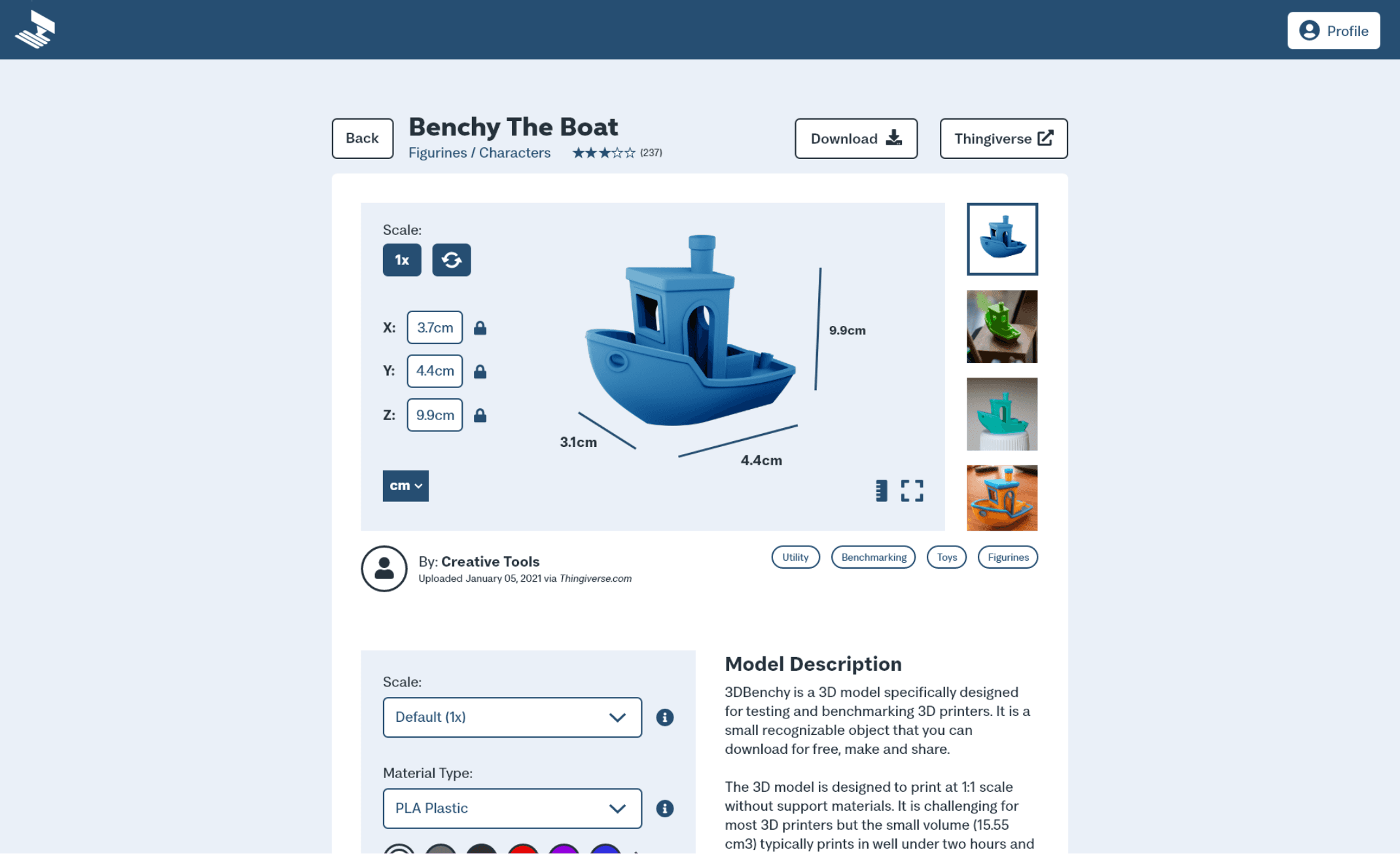
Maker Journey - File Checking (Low-Fi)
Phase 1
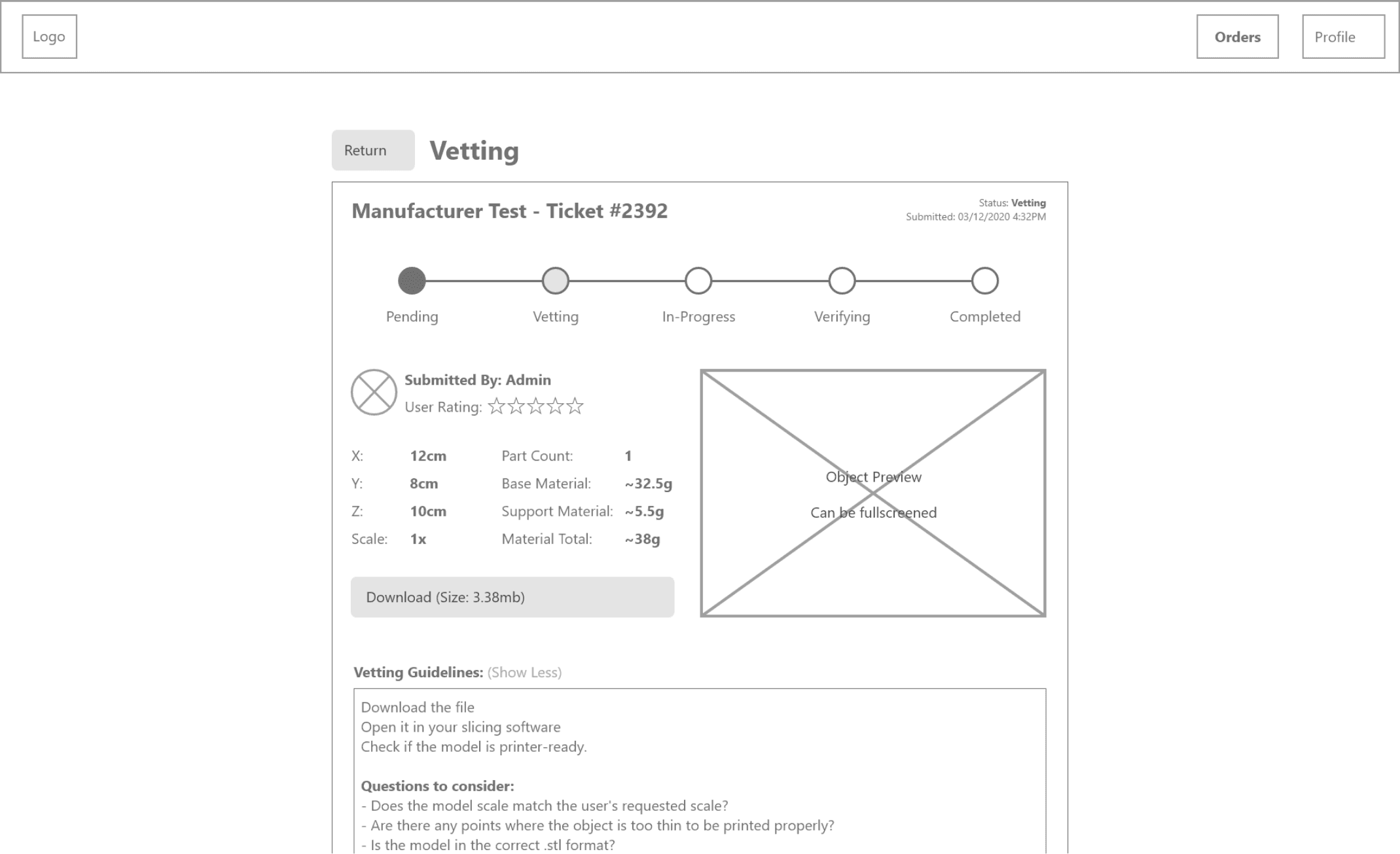
Maker Journey - File Checking (High-Fi)
Phase 2
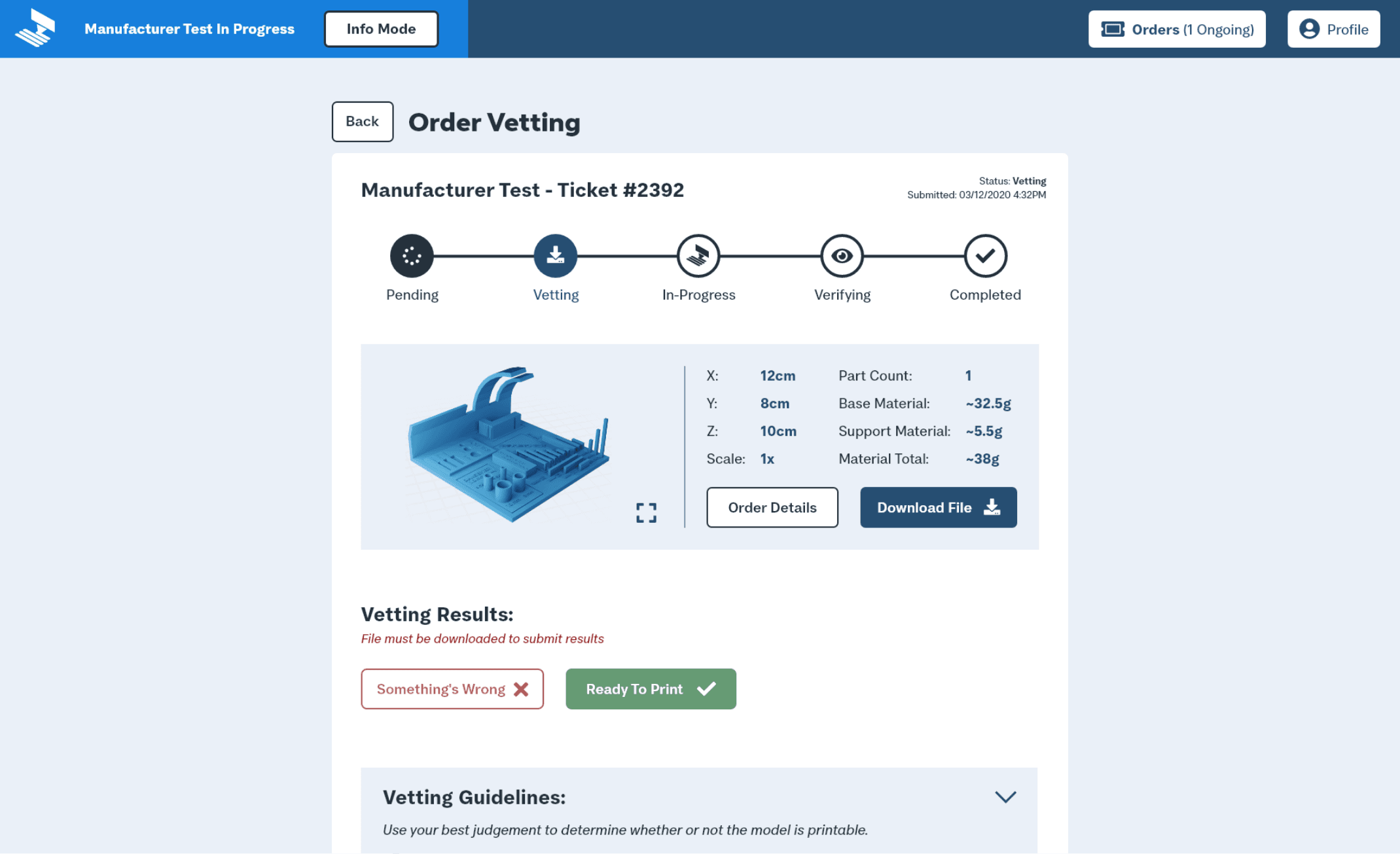
NOTABLE FEEDBACK CHANGES
Significant issues addressed during testing and revision:
Some changes were a structural shift in the service’s rules and mechanics, others were simply UI and UX improvements.
Here is a smattering of the most notable issues addressed along the way.
The Manufacturer Overview
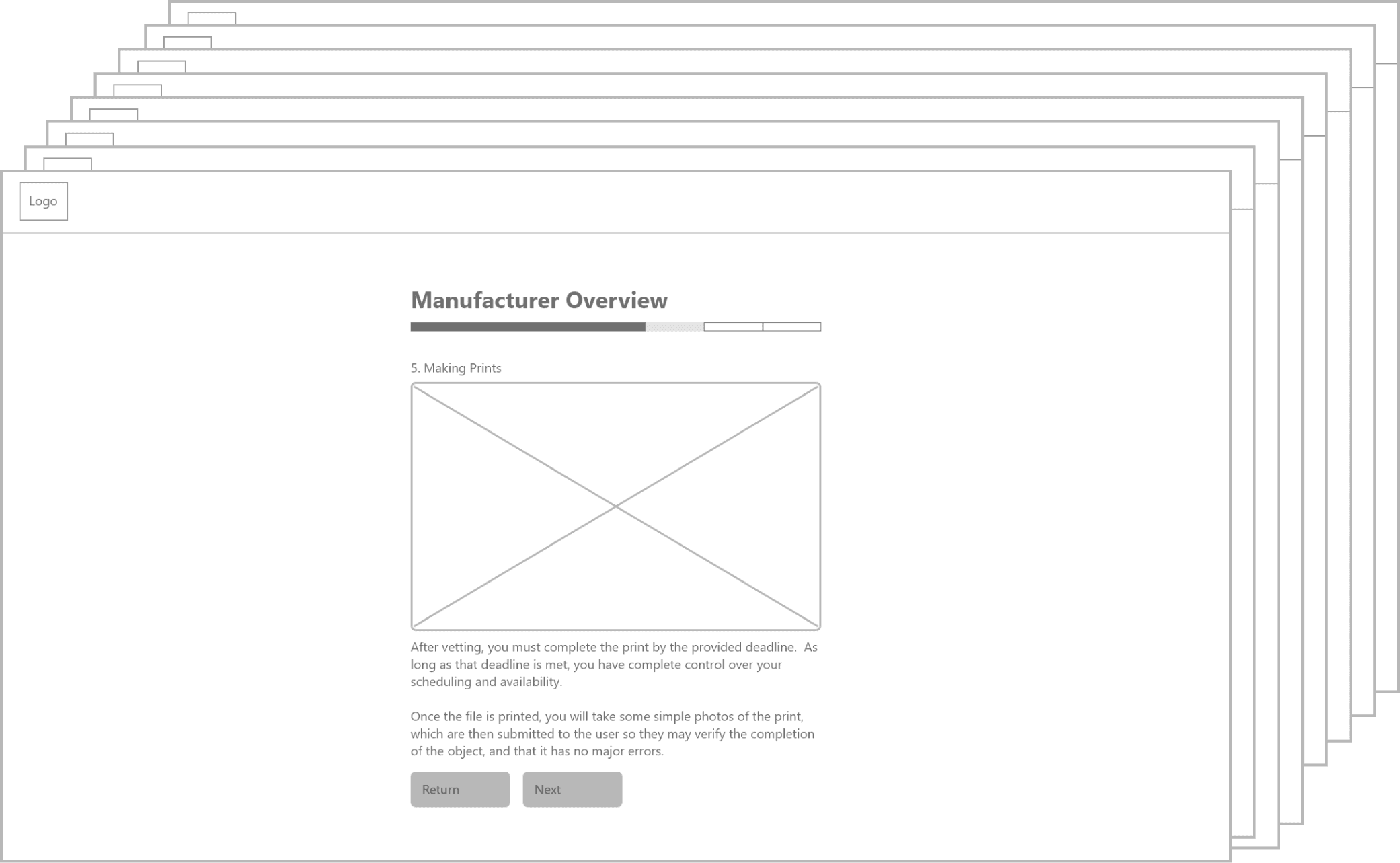
Aspiring makers need to understand the expectations of their new job. Originally, this was taught with an 8-page slideshow. But users found it droning, hard to retain, and too easy to skip.
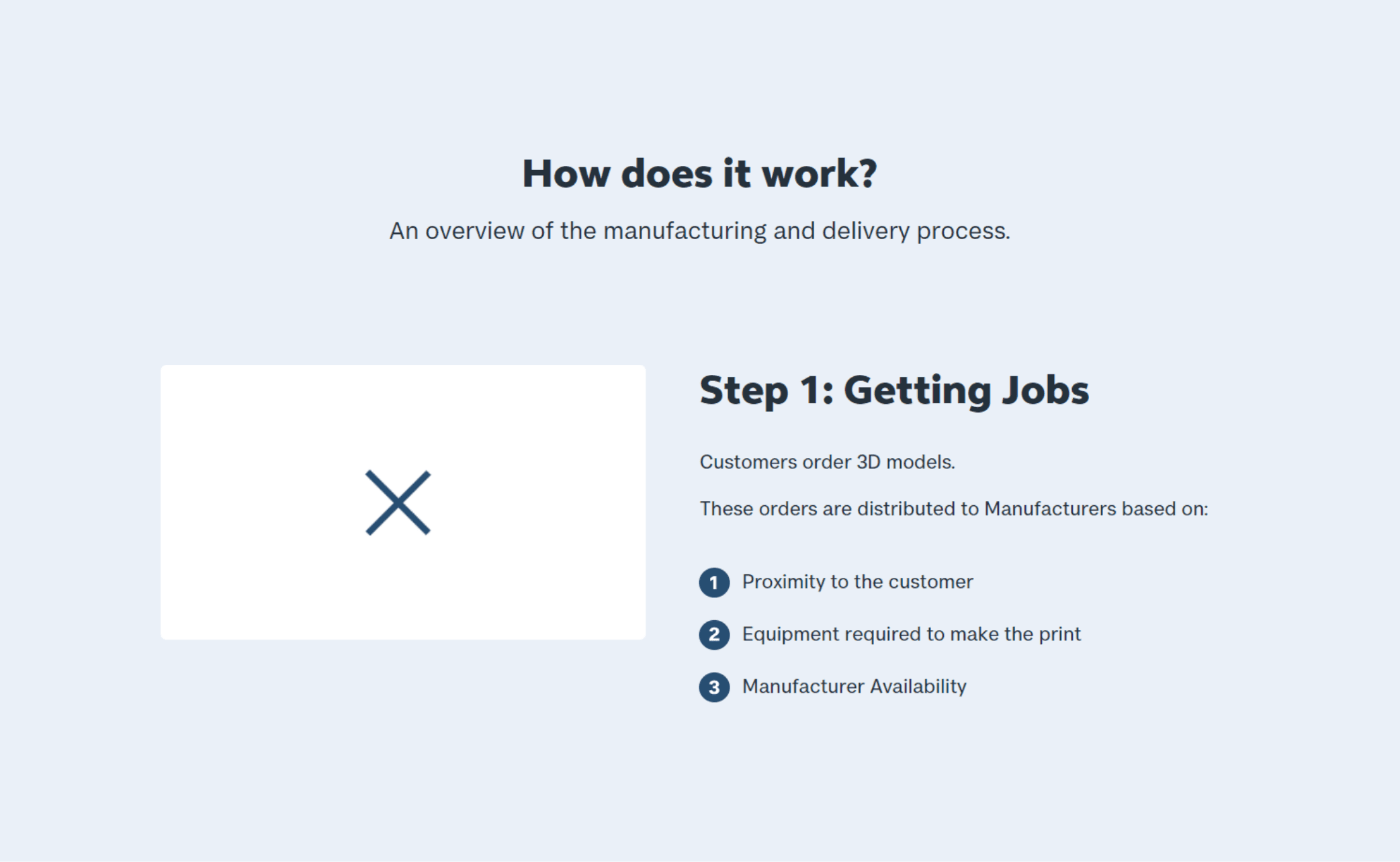
Now, that info exists as a single inviting page. As well, I added a brief video chat at the end of onboarding to ensure new Makers have read the overview, and can ask questions.
Equipment verification
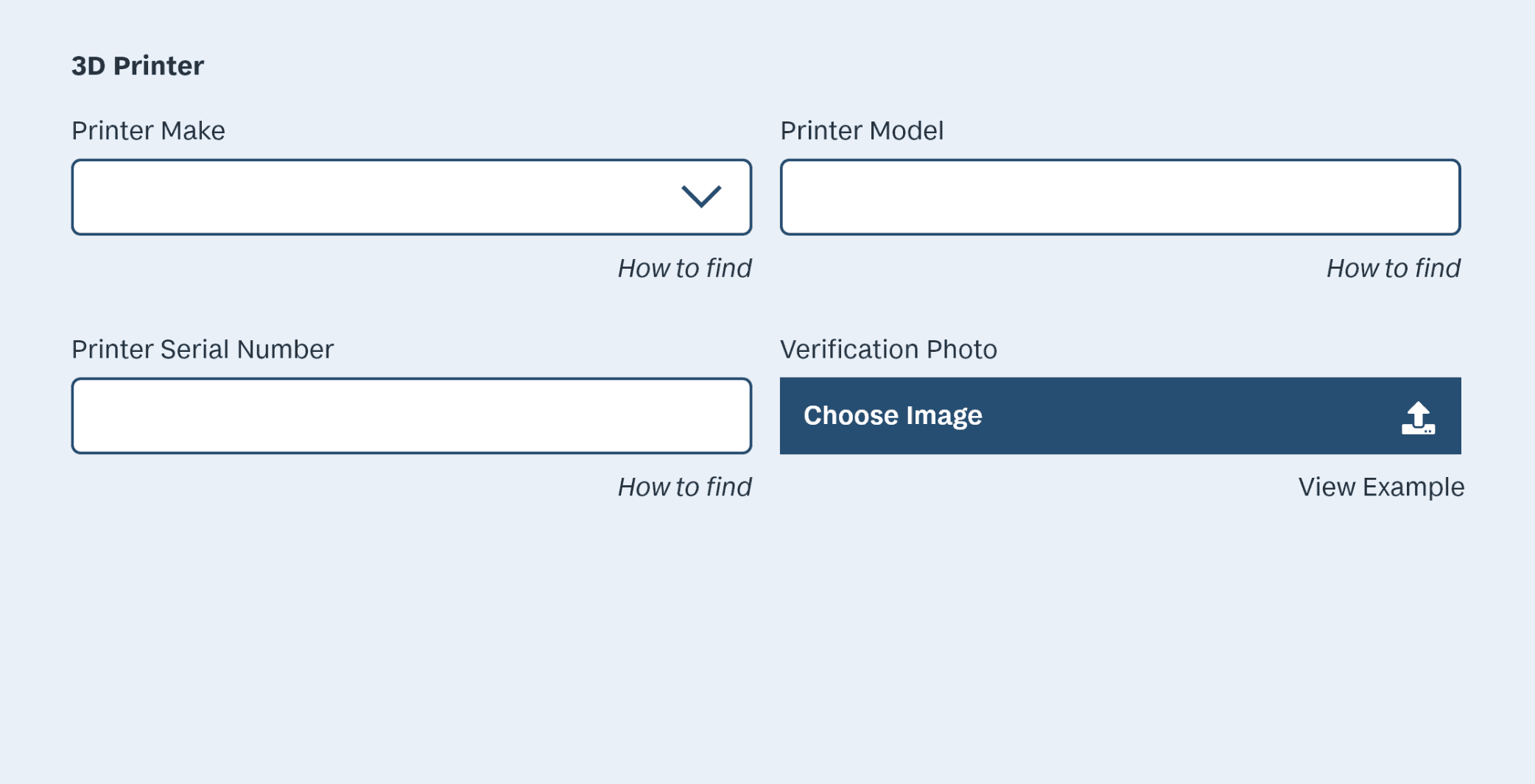
Users noted: lack of parity between printer and filament inputs, and the inability to add multiple printers.
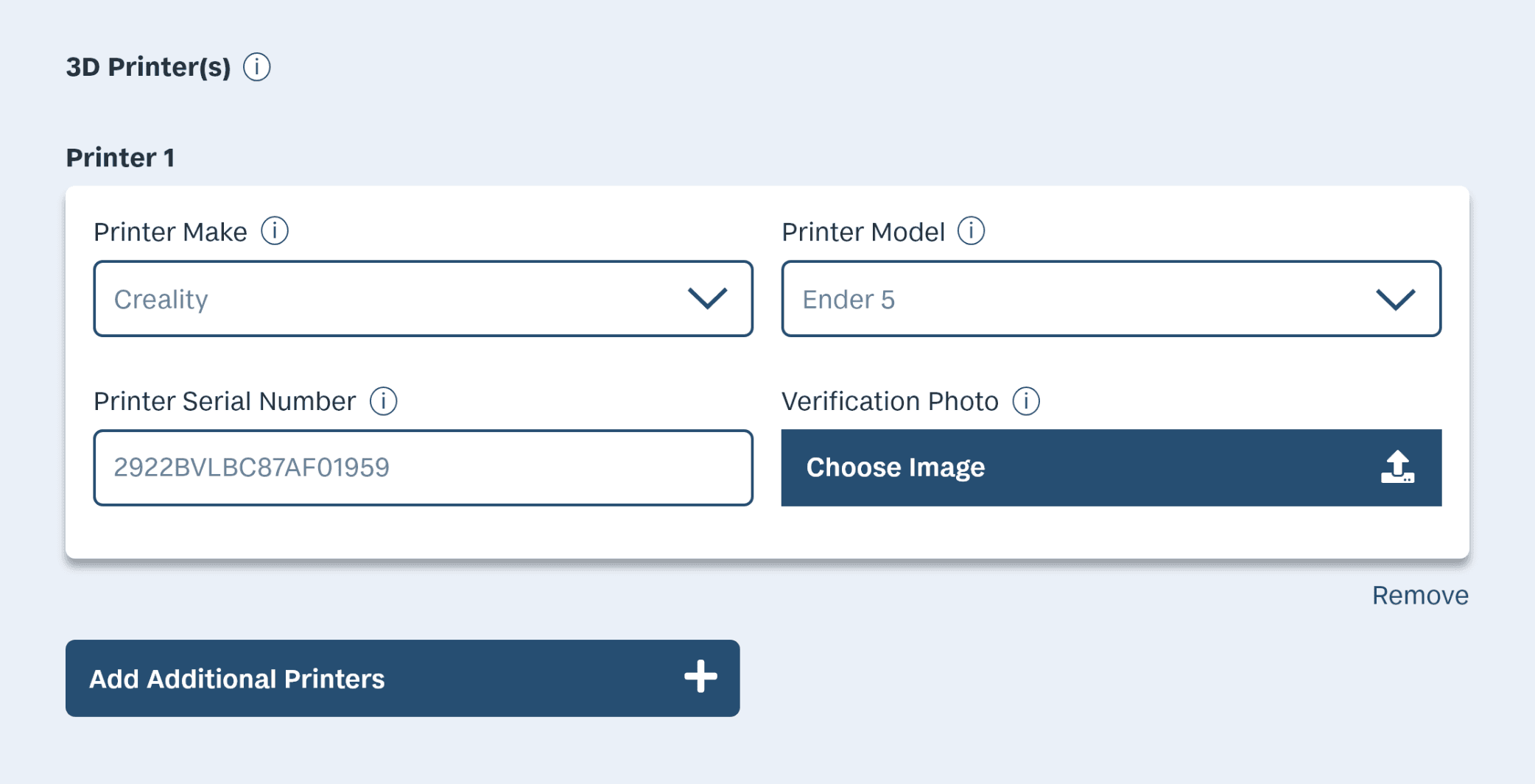
Redesign to match filament inputs, now with support for multiple printers, and integrated support via tooltips.
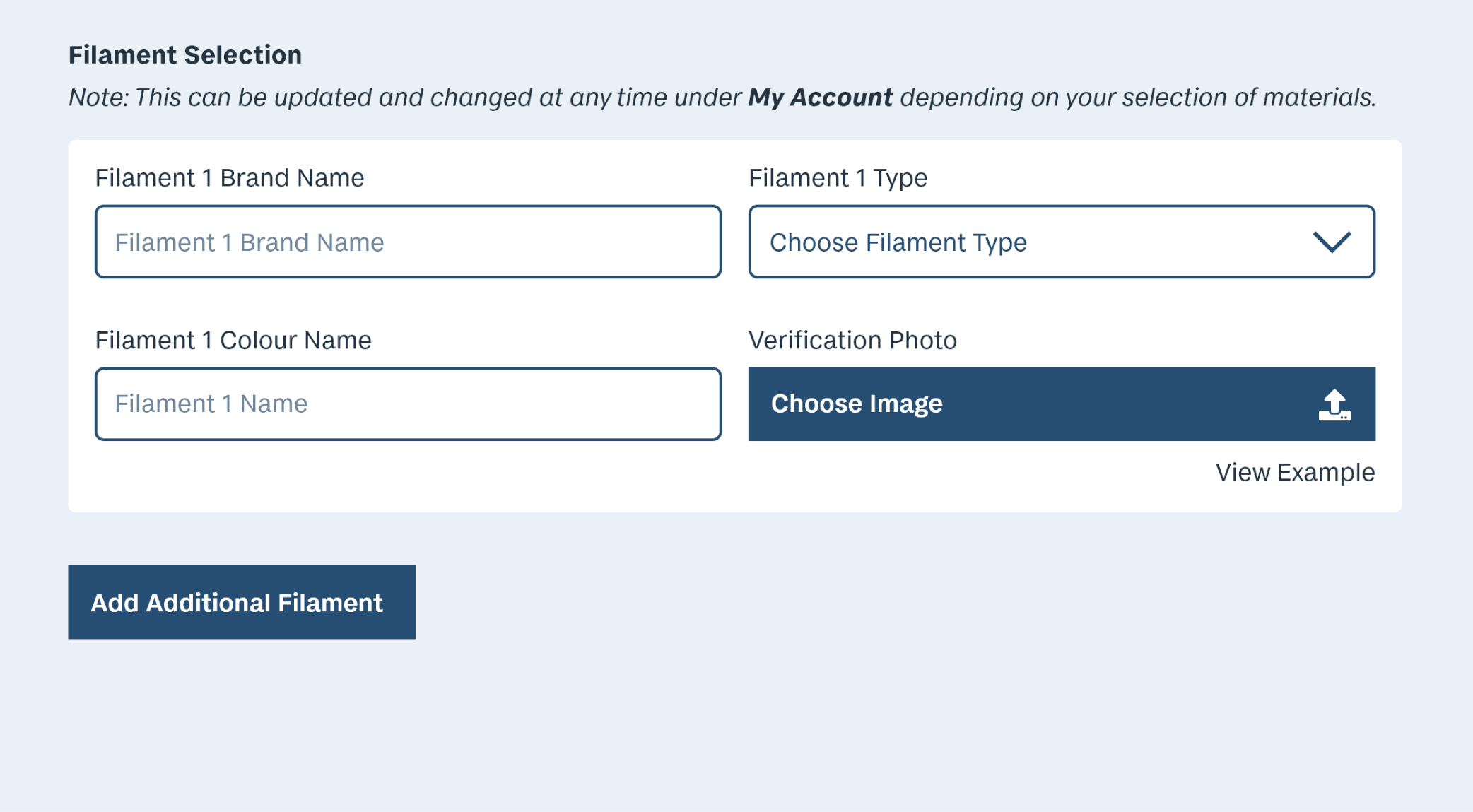
Makers may have entire shelves of filament, so it would be useful to have more distinction between each added material.
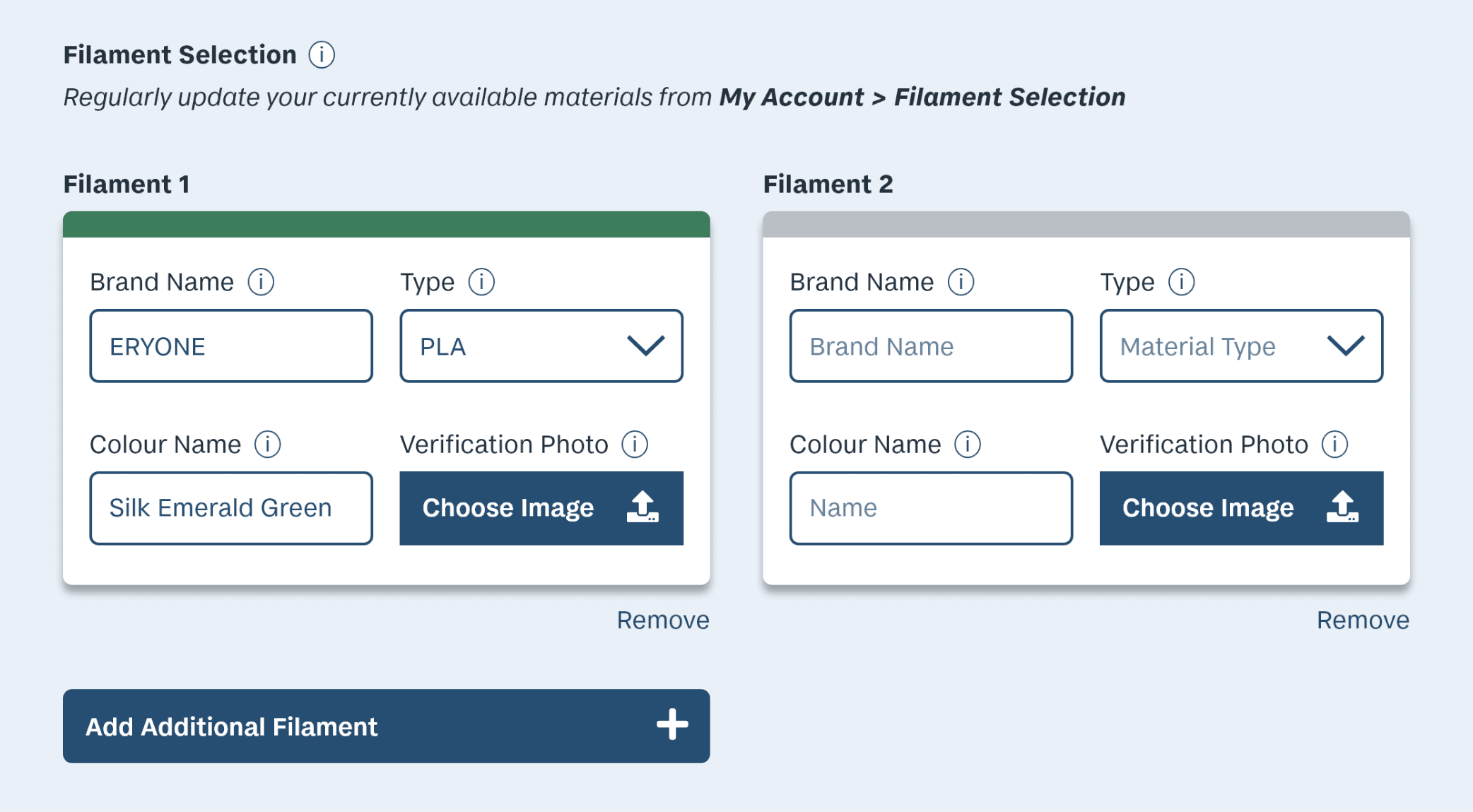
A stripe across the top of the cards match the real-world color of the inputted filament; making them much easier to differentiate.
Tutorial system
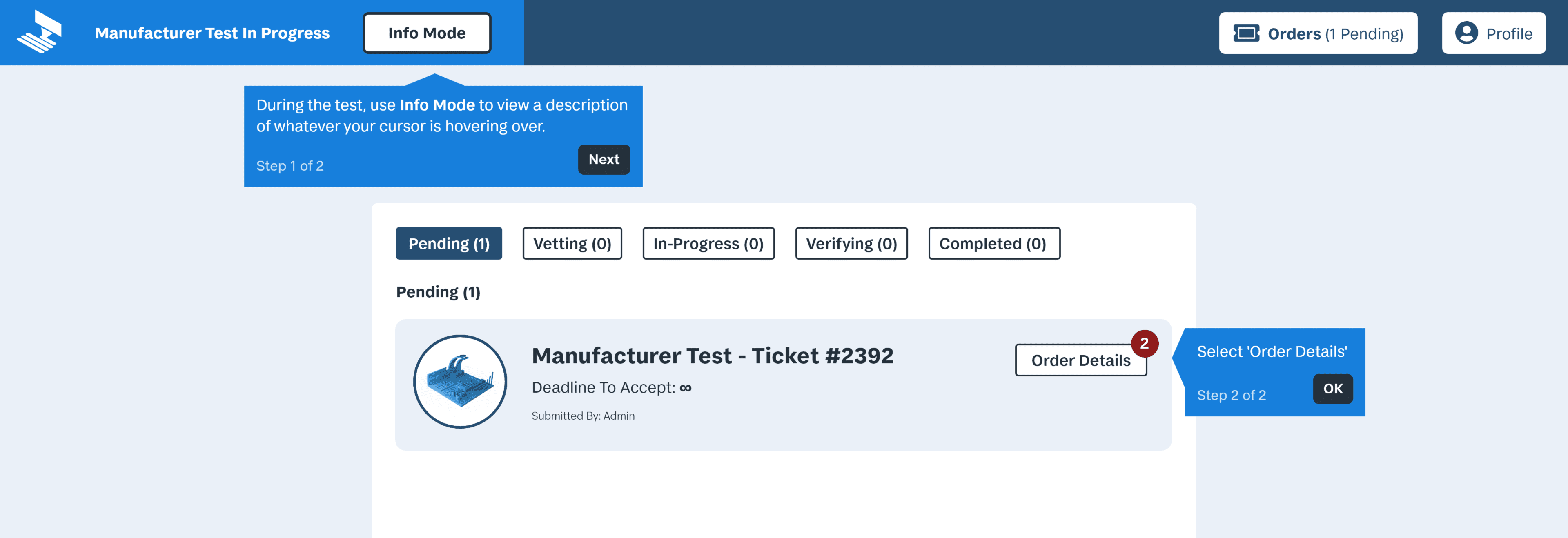
Testers of the Maker journey were navigating much more fluidly halfway through each test. It was taking a few pages of exploration before the terminology, and flow, finally clicked.
To ease the friction of a user’s first order fulfillment, I added an optional tutorial system. Boxes appear one by one describing important elements, and directing the user through their task.
With these and many other issues addressed,
I had actualized the core functionality of the service.
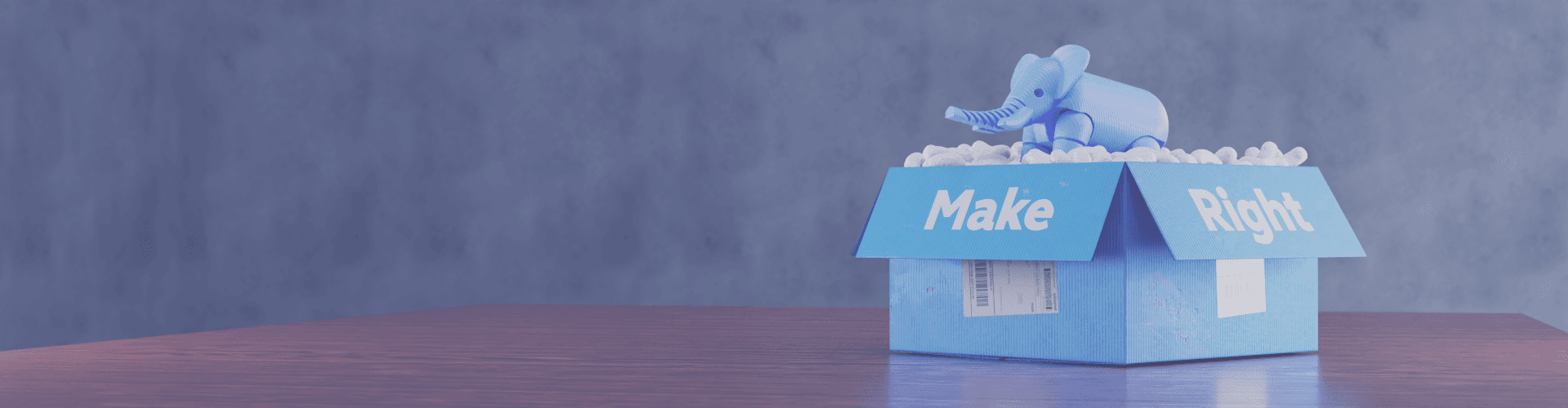
Delivered Project
Bringing 3D printing to everyday consumers
Connecting consumers to local hobbyist makers for cheap, customizable manufacturing
A browsable online storefront of ready-to-print 3D models, sourced from around the internet
Enabling makers to profit off of their equipment and skills in their spare time
Going Forward
With every feature added, countless more had to be sidelined for the sake of scope. Some of these improvements to the project include:
- A full branding refresh (the logo and name are temporary)
- Wider testing with relevant users, both customers and makers
- Overhauling the visuals and UX of the store page
- UX of user profiles
- Real-world tests with owners of 3D printers
Several team members would need to be added in order to become a dedicated company. Like algorithm engineers to help design the systems that assign orders to makers, and determine how much they get paid per job. Other additions include:
- More UX designers
- Wider testing with relevant users, both customers and makers
- Backend developers (some with cyber-security experience)
- Financial advisors
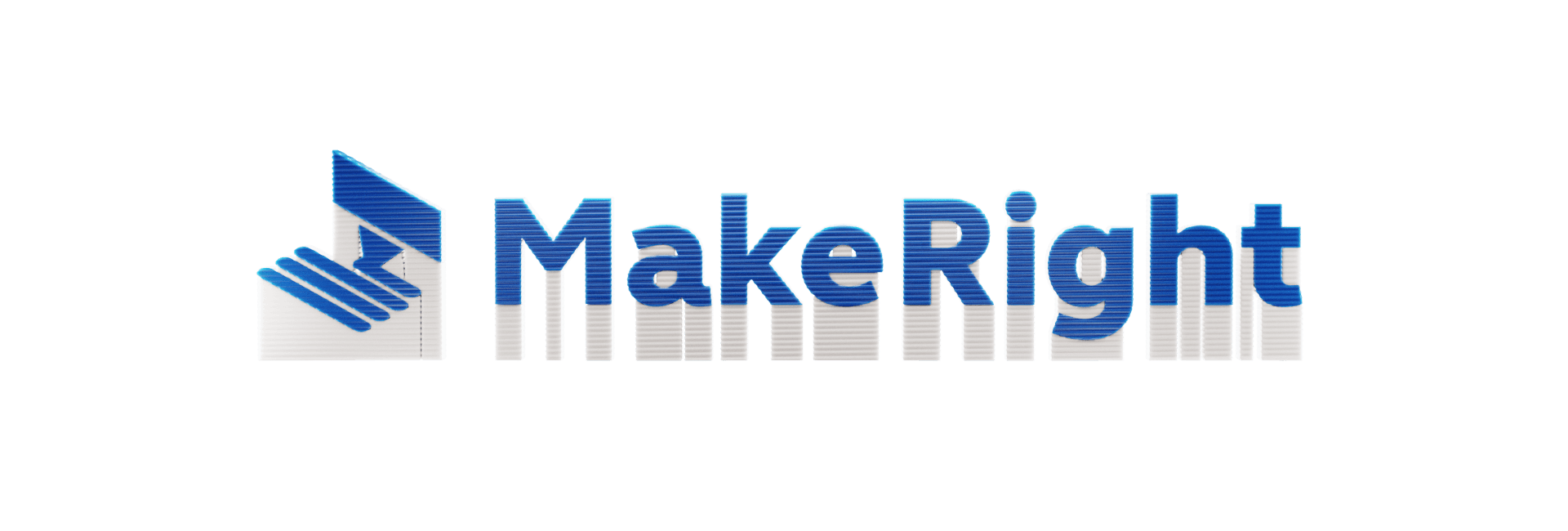
AREAS OF GROWTH
Considering entire userflows and journeys
makes for far better UI than individual features
When I began planning my approach to prototyping, I chose a number of the service’s most important features. From there, I intended to create mockups of each. Eventually, I reached the question of how the service would verify that a maker was capable and trustworthy. My solution was to have them create a mock customer order. But to prototype this, I would need to mock up the entire order fulfillment process. Only having a few select screens would be too disjointed.
At this moment, I decided the only way to consider all aspects of the service would be to build the 2 entire user flows. This caused a massive shift in my project approach. It allowed me to encounter numerous issues that would have gone unaddressed if I had only created separate feature screens.
This moment reminds me to always focus on the entire context of a user’s journey and experience. I need to avoid fixating on individual features without remembering the greater context of the system in which I’m working. Good UX design isn’t separated features in a vacuum, it’s the creation of an entire experience.
LEARNING
The importance of involving users as early, and as often as possible
In this project, I spoke with 10 potential users, in two separate groups before becoming invested in any concept or solution. This gave me important background information from which to build ideas. But equally valuable was my decision to involve this group once again after I had developed an idea. This allowed me to gather feedback on my concept, before having created any semblance of a prototype. This provided tangible validation that my ideas were worth pursuing, and a foundation of user feedback from which to expand and build.
This moment reminded me to always involve users as early and as often as possible. Often, designers forgo interviewing users in a project’s early stages. This is usually done in favour of instead testing before ideation, or after a prototype has been actualized. But, by keeping users close to my project at every stage, my solution became tailor-fitted to the exact problem that I had observed in the 3D printing space.
SUCCESSES
Creating actionable steps to achieving the core functionality of the service
I often questioned what the final outcome of this project should be. I felt strongly about this concept, and I needed to do it justice. Around the end of the first month, after much planning and revision, I had defined my goal of creating 2 user journey prototypes. With this finally established, I quickly fell into the groove of cycling through iterations week by week. I made screens, found testers, gathered feedback, implemented changes, and repeated. In the end, all the pieces fell together. Resulting in a polished, cohesive execution of my idea.
Despite many challenging time crunches during development, I steadily moved through each phase without any major snags. Working with a clear end goal, and defining actionable steps to reach it, is what brought this project to life. For this reason, the planning and organization of this project was its greatest success.